Founded in 1991, Midwest Engineered Systems (MWES) is a system integrator known for its innovative approach across a diverse range of industries, including logistics, healthcare, material handling, aerospace, and the rapidly evolving semiconductor sector. MWES specializes in high-complexity projects that many others hesitate to take on, leveraging decades of experience and deep expertise in robotics and automation to meet their customers’ custom needs.
In fact, MWES emphasizes a hands-on, collaborative approach, particularly in complex automation projects. “We do more than implement solutions. We work closely with the customer every step of the way, sometimes redesigning products to support improvements for automation. Our diverse team of engineers allows this collaborative problem-solving approach”, explains John Simons, Sales Engineer at MWES.
The challenge
A leading industrial manufacturer approached MWES with a high-stakes challenge: automating the precise pick-and-place handling of large, heavy sheets. This process involved lifting, positioning, and transporting massive components with high precision and reliability. The project called for the deployment of one of the largest FANUC® robots available: the M-2000iA/900L.
This robot alone weighed an impressive 9,600 kg and had a maximum load capacity of 900 kg, requiring a system capable of supporting its substantial weight and operational load without compromising performance. The challenge was to expand the robot’s range of motion while ensuring it could operate efficiently and continuously under these demanding conditions. Additionally, the system had to maintain reliability and speed, two critical factors in material handling.
The solution: Rollon’s RTU system
To meet these demanding requirements, MWES partnered with Rollon, a leader in linear motion and automation solutions. Rollon provided a 10-meter-long steel RTUn-2000 that was engineered to withstand both the substantial weight of the FANUC robot and the heavy materials it would handle. Its modular design helped ensuring flexibility, allowing easy customization for varying lengths and operational needs. In addition, it features low-maintenance components, which help minimize downtime and reduce operational costs.
This RTU significantly extended the robot’s operational range, allowing it to reach more work areas without the need for repositioning. The RTUn-2000’s sturdy steel construction enabled reliable performance under high loads and with minimal maintenance, helping ensure long-term durability and efficiency. This integration was a key factor in helping the customer enhance their pick-and-place operations, optimizing speed, safety, and precision.
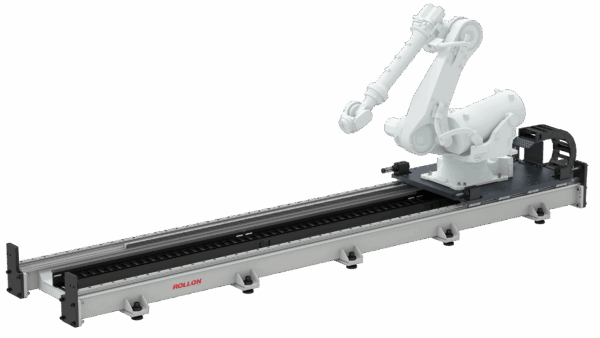
Rollon’s RTUn with steel body and rack-and-pinion drive.
Nicole Gabelbauer, Marketing Manager at MWES, elaborated on the strategic role of automation in material handling: “At MWES, we understand how critical efficient material handling is in today’s fast-paced manufacturing environment. Our custom automation solutions not only boost productivity but also create a safer workplace by reducing the risks associated with manual material handling. Partnering with experts like Rollon and MWES ensures that manufacturers get the right technology and expertise to optimize their operations.”
A collaborative partnership
The long-standing relationship between MWES and Rollon has been built on shared values of innovation, expertise, and a commitment to push boundaries. MWES sees Rollon as more than just a supplier; they value Rollon’s collaborative approach and willingness to tackle challenges that others might deem impossible.
“Our collaboration with Rollon goes back many years,” says John Simons. “We recognized Rollon’s expertise and their willingness to try solutions that others might view as unattainable. They have the same entrepreneurial, can-do attitude that we pride ourselves on here at MWES. This shared vision has helped us tackle complex projects, ultimately delivering value to our customers.”
Results
Thanks to the synergy between MWES’s engineering expertise and Rollon’s high-quality linear motion solutions, the project succeeded in fully automating the customer’s pick-and-place operations, delivering measurable improvements in productivity, accuracy, and safety. The solution provided by Rollon not only met the customer’s immediate needs, but also laid the groundwork for future scalability and adaptability as their automation requirements evolve.
For MWES, partnering with Rollon reinforces their commitment to innovation and customer satisfaction, allowing them to continue delivering custom solutions that redefine what’s possible in automation.
Notes: for EMEA Market please refer to Steel RTU.
For more information on Rollon’s linear motion solutions and to connect with Rollon application engineers in your area or region, please get in touch with us.