The implementation of safety measures in the production environment, such as barriers, cages and fences, is – if required by the outcome of the risk assessment – mandatory in order to safely integrate automated systems and enjoy the benefit in terms of productivity, efficiency and consistency that automation provides to businesses. However, the level of saturation of the layout is often such that the installation of fences requires careful planning and calculation of available space.
Linear movement systems allow fences to be integrated, reducing floor space consumption while ensuring smooth and efficient closures.
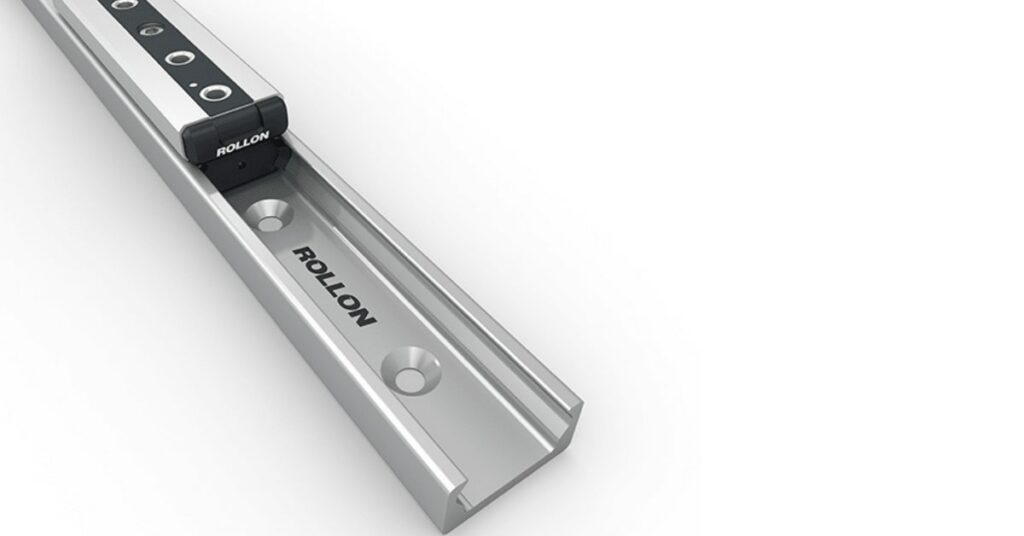
Linear guides: a case study
Youngblood Automation, a company specializing in the production of fences and guards for manufacturing machinery, turned to Rollon to develop a system for handling its Maytec solution, a system of mobile extruded aluminum panels combined with fixed fences.
Linear motion solutions had to ensure compliance with a set of stringent parameters in terms of supported load, smoothness of movement and misalignment management. In addition, the guides had to ensure the return in position of the panel near the fence with maximum precision to ensure a complete closure of the gap.
Maytec was implemented with a cantilevered configuration that required the rails to carry a load of at least 136 Newtons per meter when the barrier was pulled out. At the same time, however, the movement had to be extremely smooth to allow the fence to be opened fully and unrestricted.
Parallelism deviations: how to manage them
Maytec profiles, given the production technology at the base, present some small deviations of parallelism between the axes that require the installation of guides able to compensate and manage them without intervening with correction works on the installation surfaces.
1) When building their sliding guards, Youngblood engineers first attach the rollers to the structural frame and then mount the rails to the back side of the mobile gate or guard panel.
2) The top rail is bolted in place while the bottom rail is “floating,” which means the panel is moved to one end and the rail bolts are tightened.
3) The panel is then moved to the other end and that end is tightened. Lastly, the panel is centered and the center is finally tightened.
This floating solution creates a very easy to implement configuration and eliminates any installation constraints while reducing the costs associated with the security application.
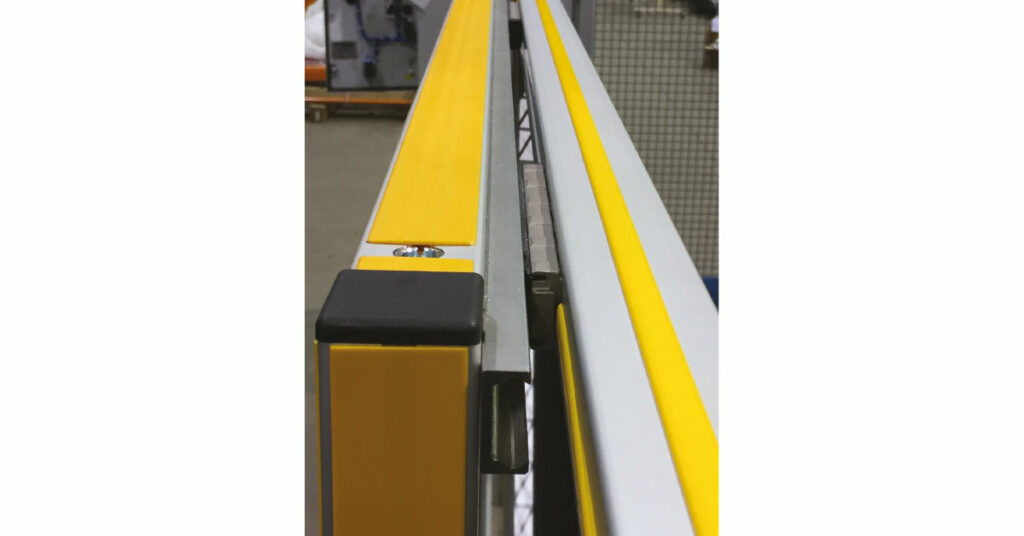
What factors drive the choice?
Youngblood chose Rollon’s Compact Rail series linear slides for this application based on a number of factors.
Weight management
The linear guides applied to the opening and closing of the panels must be able to easily handle weights along the radial or axial directions (depending on the chosen orientation, which can be parallel to the sliding plane at the top and perpendicular to the same plane at the bottom, or vice versa) and ensure that the door remains in the closed position. Compact Rail series rails are capable of handling loads/momentum up to 15,000 N.
Misalignment management
The ability of the guide itself to handle inaccuracies and misalignments (both in terms of parallelism and complanarity) arising directly from the conditions of the mounting surfaces is critical given Maytec’s characteristics. A linear bearing guide enables sliding doors to be installed with the necessary precision without the need for costly and time-consuming surface grinding. The result is a simpler yet more economical installation.
The ability to operate in difficult environments
Finally, another of the features to consider, is the ability of the linear guide to resist contaminants that are generated near the machine around which the fences are installed. There are two aspects to consider:
1. the ability to manage friction and residue on the track
2. the ability to resist corrosion or oxidation that can be generated in the production environment.
The first aspect is tackled by Compact Rail by adopting larger rolling pins (up to one inch in diameter) that allow the slider to easily overcome any obstacles present on the raceway, without jamming, suffering from wear or compromising the efficiency of the locking system.
Secondly, the integration of a combined lubrication and track cleaning system keeps the system running smoothly.
The second aspect is addressed with the availability of any surface treatments applied to the raceway, a solution that is of decisive importance depending on the environment in which the raceway operates.
If the processing exposes the rail to corrosive agents, it is necessary that the rail offers adequate resistance characteristics, such as those offered by electro-galvanizing and nickel-plating treatments.
Would you like to know more about the advantages of Rollon’s Compact Rail series? Contact one of our experts