In modern industry, automation is essential for enhancing productivity, efficiency, and process precision. The industrial robotic arm is a vital tool in various applications, from material handling to welding, assembly, and logistics. However, traditional six-axis industrial robots face limitations in reach and flexibility, as their movement is confined to a fixed area.
To overcome these limitations, Rollon has developed a system that provides a seventh axis of movement, allowing robotic arms to travel along a linear unit.
Why does a robotic arm need a seventh axis?
Adding a seventh axis, essentially a linear translation unit, extends the robot’s operational range, enabling it to cover multiple work areas or move between different stations without requiring additional robotic units. This linear component, mounted on a guide, allows the robotic arm to glide along a track, transforming it into a more dynamic and versatile system.
This expanded mobility is particularly advantageous in large-scale production environments, where the robot must perform repetitive tasks at multiple points along the line. Adding a seventh axis turns an industrial robotic arm into an even more versatile machine, capable of covering large work areas with smooth, precise movements, thereby boosting productivity and reducing operating costs.
How do Rollon’s seventh-axis work?
Rollon’s RTUs are designed to provide a seventh beam to industrial robotic arms, allowing them to move along a track and thus extending their range of motion. These RTUs are designed for high-load anthropomorphic robots, offering a highly customisable solution for advanced industrial applications. The system is based on a carriage on which the robot is mounted, driven by a rack and pinion, and guided by recirculating ball guides, rollers or bearings. A highly efficient solution offering smooth, precise and vibration-free movements, even under high loads, over long distances, and in the harshest environments.
A further advantage of Rollon’s Robot Transfer Unit system is that, being driven by a Rack and pinion, there is the possibility of potentially infinite Strokes thanks to the jointed and self-centring inserts. This means that it is potentially possible to connect several six-axis robots on a single seventh beam, allowing them to operate independently. In this way, a single system can handle multiple operations simultaneously, increasing productivity and optimising the use of space in automated production lines.
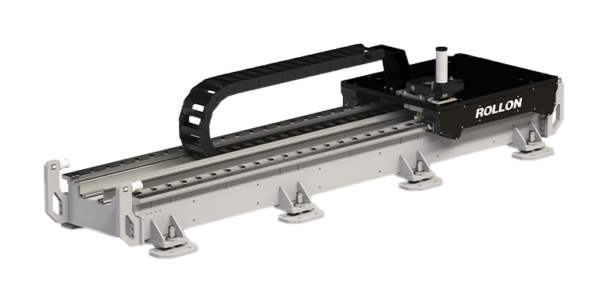
Industrial applications: where are robotic arms with a seventh axis used?
Regardless of the size or weight of the industrial robotic arm, each Rollon model is designed to meet specific needs, adapting to different types of robots:
- RTU Open Belt: robot transfer unit with aluminium body and belt drive for small industrial robots. The carriage slides on two parallel linear guides with four self-lubricated recirculating ball guides, positioned to support the carriage and all loads and load moments.
- RTU Sealed Belt : robot transfer unit suitable for dirty environments, with aluminium body and driving belt for small industrial robots. Equipped with a polyurethane sealing strip to protect all internal components from dust, contaminants and other foreign objects.
- RTU Rack & Pinion: robot transfer unit with aluminium body, Rack and pinion drive for robots up to 1500 kg. The robot transfer unit consists of one or two self-supporting profiles made of extruded aluminium AL 6060 T6 joined together by means of rigid crossbars.
- RTUn: Uncovered robot transfer unit with steel body and Rack and pinion transmission. Available for small and large industrial robots. Available with recirculating roller guides or Tapered roller bearing guides for the most demanding environments and to compensate for surface misalignment errors.
In addition to the variety of models, Rollon’s seventh axis offer flexible mounting options, being able to be installed on the floor, wall or upside down on the ceiling, with mounting holders and levelling feet ensuring safe installation. For applications where operators must walk on the beam, Rollon provides a diamond plate cover, reducing the risk of tripping. Each system can be customised with Cable carriers, Proximity switches and rubber decelerators, offering seamless integration into the most advanced industrial applications.
FAQs
What is the difference between a robot arm and a Cobot?
A robot arm is an automated, programmable device designed for industrial tasks, while a cobot (collaborative robot) works alongside humans safely without protective barriers.
What are the types of robotic arm designs?
The main types of robotic arm designs include articulated, cartesian, cylindrical, SCARA, delta, and polar configurations, each suited for specific tasks and environments.