Automated warehouse systems are leading the way in logistics automation. Among the most efficient solutions are automated warehouses, particularly vertical systems, designed to maximize vertical space while ensuring quick and secure access to stored goods.
In this article, we will explore how linear guide technologies, such as Speedy Rail, ball bearing telescopic guides and SAR+SAR multi-axis YZ systems, can improve handling within an automated warehouse, reducing operational risks and increasing productivity.
What is an automated warehouse and how does it work
An automated warehouse is a storage system that manages the handling of goods in an automated way. Unlike traditional warehouses, automated warehouses are managed by integrated software that controls every phase of the process.
Vertical automated warehouses, in particular, store products on high shelving units, while automated warehouse robots, such as stacker cranes and Cartesian robots, handle picking and placement. This approach not only increases storage capacity but also improves safety by eliminating the need for workers to access high storage areas manually.
Linear and telescopic guides in automated warehouses
Linear and telescopic rails are essential for the smooth operation of automated warehouse systems. These components enable precise, frictionless movement of shuttles, picking devices, and automated warehouse robots, ensuring consistent performance even in high-demand environments.
The use of high-quality components, such as Speedy Rail, improves operational efficiency while reducing maintenance costs thanks to their robust, self-supporting and maintenance-free structure.
Speedy Rail is an extremely versatile linear guide rail with an anodised aluminium profile and polymer-coated steel roller bearings that slide directly on the profile, thus eliminating the need for lubrication.
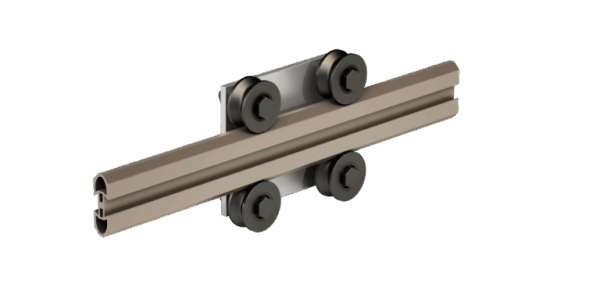
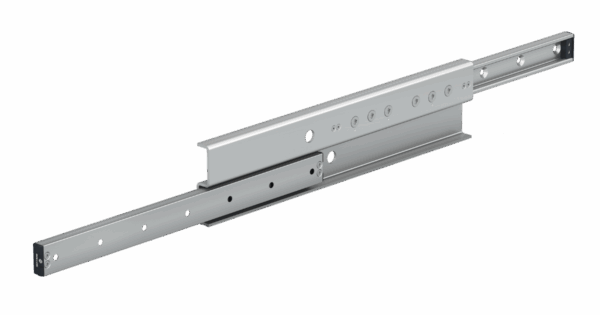
Self-supporting guides to minimize risk
Self-supporting and motorized guide rails, such as Speedy Rail SAR, offer greater structural stability, reducing the risk of misalignment and failure in automated handling systems. Thanks to their robust and self-supporting design, they offer high load capacity and reliable operation even in difficult environments, with resistance to dust, dirt and wear. Furthermore, their ability to absorb vibrations and shocks contributes to extending the equipment’s lifetime, improving the system’s overall reliability and reducing maintenance costs.
In automatic vertical warehouses, the integration of a Y/Z-axis multi-system, such as SAR+SAR, is essential to optimise handling between shelves. This system allows the automatic shuttles to move quickly both horizontally and vertically, ensuring fast and precise access to stored materials. The result? Reduced picking and deposit times, increased productivity and more efficient stock management, minimising downtime and increasing warehouse operational flow.
By combining advanced linear solutions such as linear guides and multi-axis systems, it is possible to optimise the handling of goods, improve the safety of operations and reduce management costs within an automatic vertical warehouse. This approach not only increases operational efficiency but also allows companies to respond more quickly to market demands, improving the level of service offered to customers.
FAQs
Do linear guides require maintenance in automated warehouses?
Linear guides used in automated warehouse systems generally require minimal maintenance, thanks to their robust design and high-quality materials. However, regular maintenance is still recommended to ensure optimal performance and longevity. Modern linear guides, such as Rollon’s Speedy Rail SAR, are designed for logistics automation environments, offering self-aligning capabilities and corrosion-resistant materials.