A high-tech company specialized in the design and production of electrical wires and connectors needed a customised curvilinear handling system to transport coils of electric wires through nine processing stations. The choice fell on Rollon® Nadella AXNRQ circular system in ring configuration.
With the continuous global rise of automated production systems, manufacturing companies face the challenge of integrating automation to maintain a competitive edge. Automation not only enhances efficiency but also improves flexibility, allowing plants to adapt quickly to new product designs and changing production demands. Moreover, automation reduces human error and ensures consistent product quality, making it a crucial investment for modern manufacturing facilities.
The challenge
A high-tech company specialized in the design and production of electrical wires and connectors needed an advanced automation solution to streamline its production process. Specifically, the company required a customized curvilinear handling system to transport coils of electric wires through nine machining stations while maintaining a cycle time of under two seconds between each stage.
Additionally, the system had to meet two other critical requirements: sufficient load capacity to handle coils of varying weights (8, 10, or 12 kg) and the ability to be installed on a 10-meter-long support structure already present inside the manufacturing plant.
With industrial automation playing an increasingly vital role in enhancing efficiency, flexibility, and product quality, finding a solution that optimized space, reduced manual intervention, and ensured high-speed operation was essential.
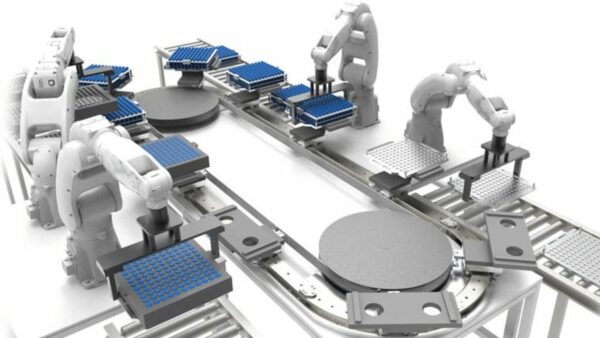
AXNRQ Application example
The solution
After a thorough analysis of the application requirements, Rollon Nadella engineers proposed the AXNRQ circular system in ring configuration. This solution was selected due to its ability to meet the key operational demands of the project, offering:
- High load capacity with robust guide rollers that support loads in all directions, helping ensure smooth and stable transportation of coils.
- Optimized acceleration and speed, meeting the stringent stroke time requirement between machining stations.
- Space-efficient design, allowing seamless integration onto the existing 10-meter-long support structure within the plant.
The system provided features a 10-meter-long circular track equipped with 24 carriages, ensuring continuous operation across all machining stations. Furthermore, to enhance reliability and minimize maintenance efforts, the solution includes an automatic lubrication system that helps ensure optimal performance over extended operational cycles.
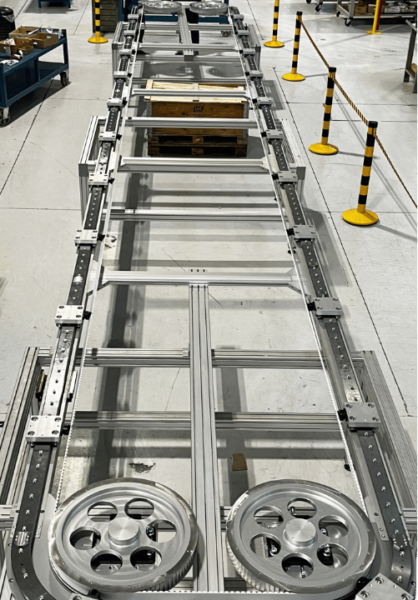
10-meter-long AXNRQ Circular System
The AXNRQ circular system delivers a fully integrated, ready-to-use circuit that allows manufacturers to achieve the desired performance while reducing footprint and engineering time. The core components of the system include:
- Aluminum base for lightweight strength and easy installation.
- Guide rails and carriages for precise and smooth movement.
- Transmission system with gearbox and toothed belt for efficient motion control.
- Lubrication units for extended durability and reduced maintenance.
- Carriage indexing system to ensure accurate positioning at each processing station.
The results
The implementation of the AXNRQ circular system has brought several benefits to the customer’s production process:
- Improved motion control: the guide rollers contribute to stable and precise movement, helping to achieve accurate positioning of the coils.
- Efficient use of space: The machined aluminum alloy base, directly connected to the gearbox, supports a compact and easy-to-install system.
- Adaptability to specific needs: The modular and configurable design allows for a tailored approach to different production setups, potentially reducing installation time and engineering effort.
By adopting Rollon Nadella’s AXNRQ circular system, the company was able to implement an automation solution that aligns with its operational requirements, supporting efficiency and productivity improvements while optimizing the use of available space.
For more information on Rollon’s linear motion solutions and to connect with Rollon application engineers in your area or region, please get in touch with us.