Railway maintenance requires precision, reliability, and above all, safety. In this article, you’ll discover how a custom-designed sliding seat mechanism featuring a linear motion system from Rollon helped technical crews improve lateral visibility aboard maintenance locomotives.
In the critical environment of rail maintenance, both safety and reliability are paramount. Often it can be the most unassuming components that deliver the biggest impact. This is the case with Rollon’s linear motion technology, which plays a critical role in enhancing visibility and safety aboard maintenance locomotives.
The challenge
Maintenance locomotives, unlike commercial trains, are purpose-built for technical crews responsible for on-track maintenance and inspection.
One of the practical challenges for optimizing safety is ensuring engineers and mechanicians working onboard the maintenance locomotives have full lateral visibility to monitor the track and surrounding environment during operations.
In earlier configurations, seating within these technical locomotives was fixed, offering limited visual range to those onboard. With limited mobility, consistently overseeing work zones posed some logistical challenges especially on both sides of the locomotive.
Therefore, a leading European train operator contacted Rollon with a clear requirement: a lateral movement system that allowed engineers to reposition themselves swiftly and securely in response to dynamic maintenance conditions.
The solution
After thorough research and problem-solving, Rollon responded with its TLC43 and ULC43 Compact Rail, a robust linear guide system that provides smooth manual adjustment of seats. Mounted onto a basic metal sheet frame, this system enables precise lateral sliding of seats while withstanding the harsh conditions typical of maintenance environments, including dust, vibration and potential sudden impacts.
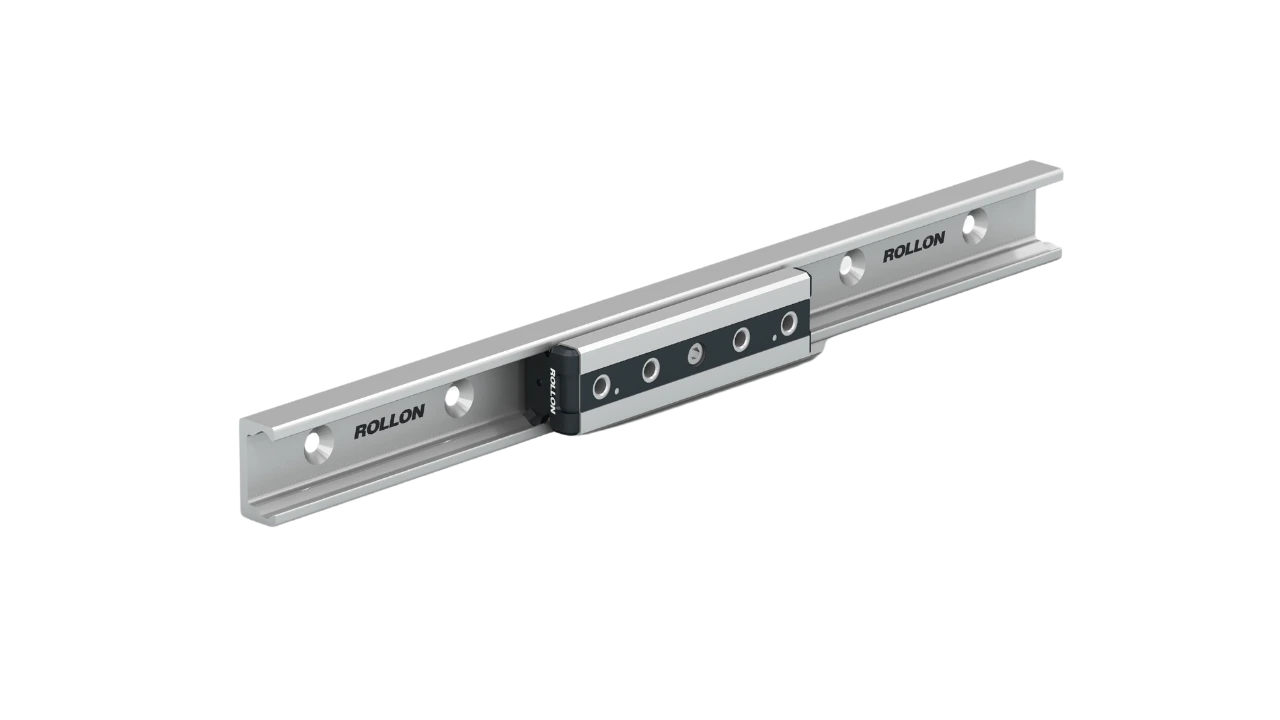
Rollon® Compact Rail
The TLC43 and ULC43 liner guide uses bearings rather than balls, making it particularly resilient in challenging settings. This choice also ensures a quieter and more fluid motion, allowing engineers to adjust position with ease without the need for power assistance. With a load rating of 150 kg under functional conditions and the capacity to endure 3G accelerations during emergency stops or abrupt movements, it is built to perform under pressure.
Crucially, Compact Rail also excels in its ability to compensate for misalignment. Unlike traditional systems that require precision-machined surfaces, Compact Rail can be mounted onto standard welded steel structures without the need for high-tolerance fabrication. This saves considerable manufacturing time and cost, offering a rugged and reliable solution that’s both efficient and affordable.
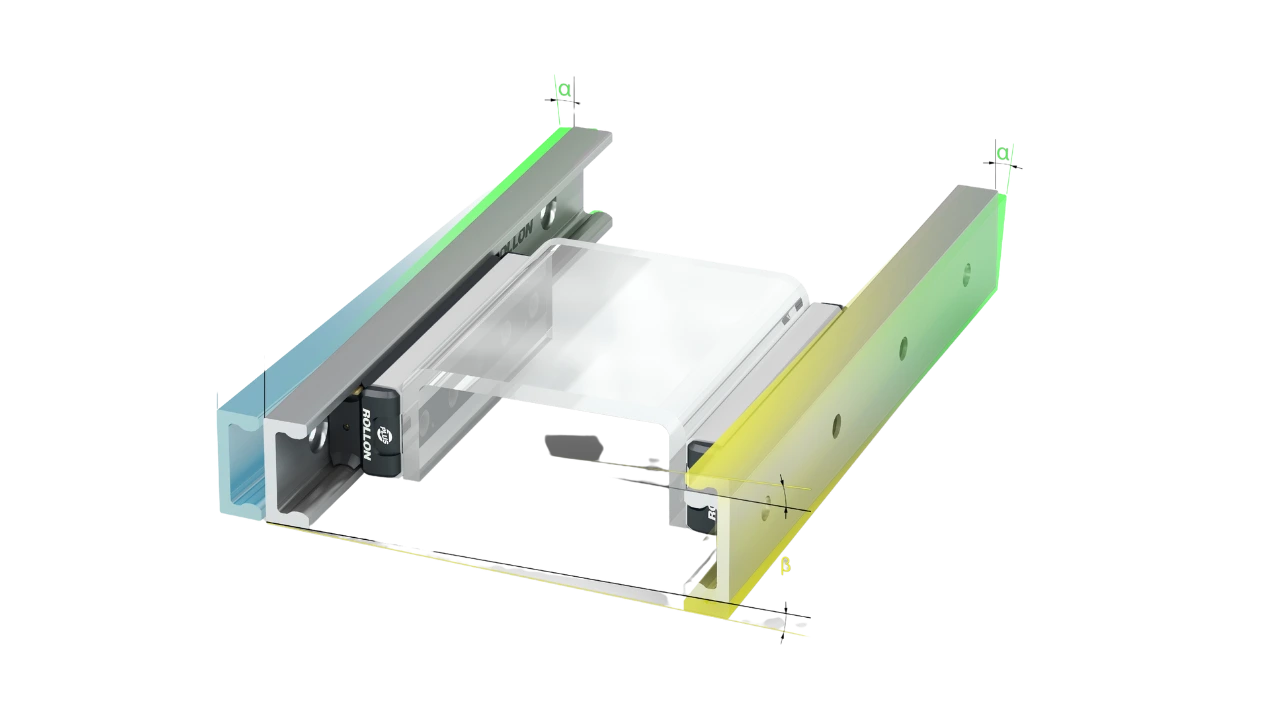
Rollon® Compact Rail can compensate for misalignment.
A simple mechanism that improves safety and usability
The sliding seat functionality is more than a convenience – it directly supports safety protocols for a safer workplace. By allowing onboard engineers to slide across to windows on either side of the locomotive, they can maintain visual contact with colleagues working outside, monitor track conditions and respond quickly to hazards.
“This type of application really shows the strength of Compact Rail technology in harsh environments,” says Antoine Salomon, Key Account Manager at Rollon. “By using ball bearings, we can offer smooth, manual adjustment that doesn’t require power assistance or complex electronics. The ability to compensate for misalignment means our customers don’t need high-precision surfaces either, which is a huge benefit in industrial and rail applications where simplicity and durability are paramount.”
“The seat adjustment system in the maintenance locomotive is a perfect example of engineering minimalism at its finest. Motors and programming aren’t required – just robust, intelligent mechanical design that solves a very human problem. Rollon’s Compact Rail system proves that you don’t need complexity to achieve functionality. You just need the right combination of engineering expertise, durability, adaptability and understanding the customer’s needs.”
This application serves as a blueprint for how small changes in motion design can yield significant gains in usability, cost-effectiveness and safety. Rollon foresees wider application of the design principles in future builds or retrofits, with each implementation refined to match the customer’s specific operational needs.
For more information on Rollon’s linear motion solutions, please get in touch with us.