Safety-stroke. When talking about safety-stroke or overtravel, we refer to the stroke needed by the customer in the event of an emergency—either in preliminary testing or within the scope of the operation. The most common example of overtravel comes during the initial phase testing and programming of a servo-driven application. Control engineers and PLC operators often test to exceed the limits of their originally-defined stroke during motion setup. Without the presence of safety-stroke, the slow speed can cause a crash.
Our linear actuators are internally-fitted with safety stops to prevent a light crash, which is typically between one and two inches per second. A crash that exceeds this speed can destroy the internal components of the actuator. For this reason, the question of safety-stroke is present when our engineers size an actuator.
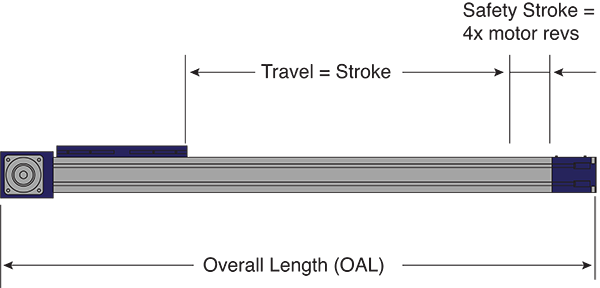
Overtravel. We set a standard for overtravel in the event that the customer can’t initially decide. The standard is based on the rule of two motor revolutions per each end of the actuator. If we consider a TH-110 actuator with a 16/5 ballscrew, we can calculate the recommended safety-stroke: 2 motor turns x 5mm/motor turn x 2 ends for a total of 20 mm or 10 mm per each end of the actuator.
If a customer who is setting up their operation inadvertently overruns their original stroke, they will have two motor revolutions—10 mm in this case—on each end to will help reduce the likelihood of crashes. In the case of a belt-driven actuator, such as our ELM series, the advised overtravel is calculated based on: 2 motor turns x lead x 2 ends / gearbox ratio.
For the ELM 80 actuator—whose lead is about 190 mm per revolution with a 10:1 gearbox ratio—the recommended safety-stroke value is 76 mm or 38 mm at each end of the actuator.