Founded in 2000, CNC Solutions began with a focus on safety enhancements for machine tools, leveraging software and machine interfaces. Over the past two decades, the company has evolved to meet the growing demands of the industrial automation sector, becoming a leader in custom robotic solutions. Today, CNC Solutions is an authorized Fanuc system integrator specializing in robotic automation for a broad range of applications across the U.S. industrial landscape, including machine tending, material removal, welding, drilling, assembly, and palletizing. “We are experts in material handling applications. One thing that sets us apart is our premier programmers. Many on our engineering staff have over 20 years of experience in the automation industry.” notes Jeffrey Wojtkiewicz, Engineering Manager at CNC Solutions.
CNC Solutions delivers end-to-end robotic process automation solutions from design through validation. Your projects typically go live within a week after installation, showing off their commitment to rapid deployment in manufacturing environments. CNC Solutions stands out as an industry leader by combining engineering expertise with strategic partnerships, particularly with Rollon’s advanced linear motion technology that powers their integrated robotic automation systems for maximum production efficiency.
The Challenge
You endure increasingly difficult material handling demands in heavy industries like oil and gas, and in a recent project, CNC Solutions tackled an ambitious automation challenge, designing and implementing a CNC automation system capable of manipulating 500-pound pipe flanges with precision.
This application requires integrating a Fanuc M-900iB/700 industrial robot, one of the most robust high-payload robots available on the market. The engineering team needed to extend the robot’s reach to service multiple production areas while maintaining exact positioning accuracy despite the extreme weight of the components.
The complexity wasn’t just in the robot’s capacity, your CNC automation solution had to deliver repeatable precision while handling these massive parts across a significant operational footprint, all while maintaining the durability needed in demanding oil and gas manufacturing environments.
“The heavy payload and large parts meant that we had to ensure structural stability. Furthermore, the solution would need to expand the robot’s operating reach to support the required working area as well,” explained Jeffrey Wojtkiewicz.
To extend the robot’s reach accurately and soundly, CNC Solutions found it imperative to have a reliable Robot Transfer Unit (RTU) capable of high load capacity and smooth performance under continuous operation.
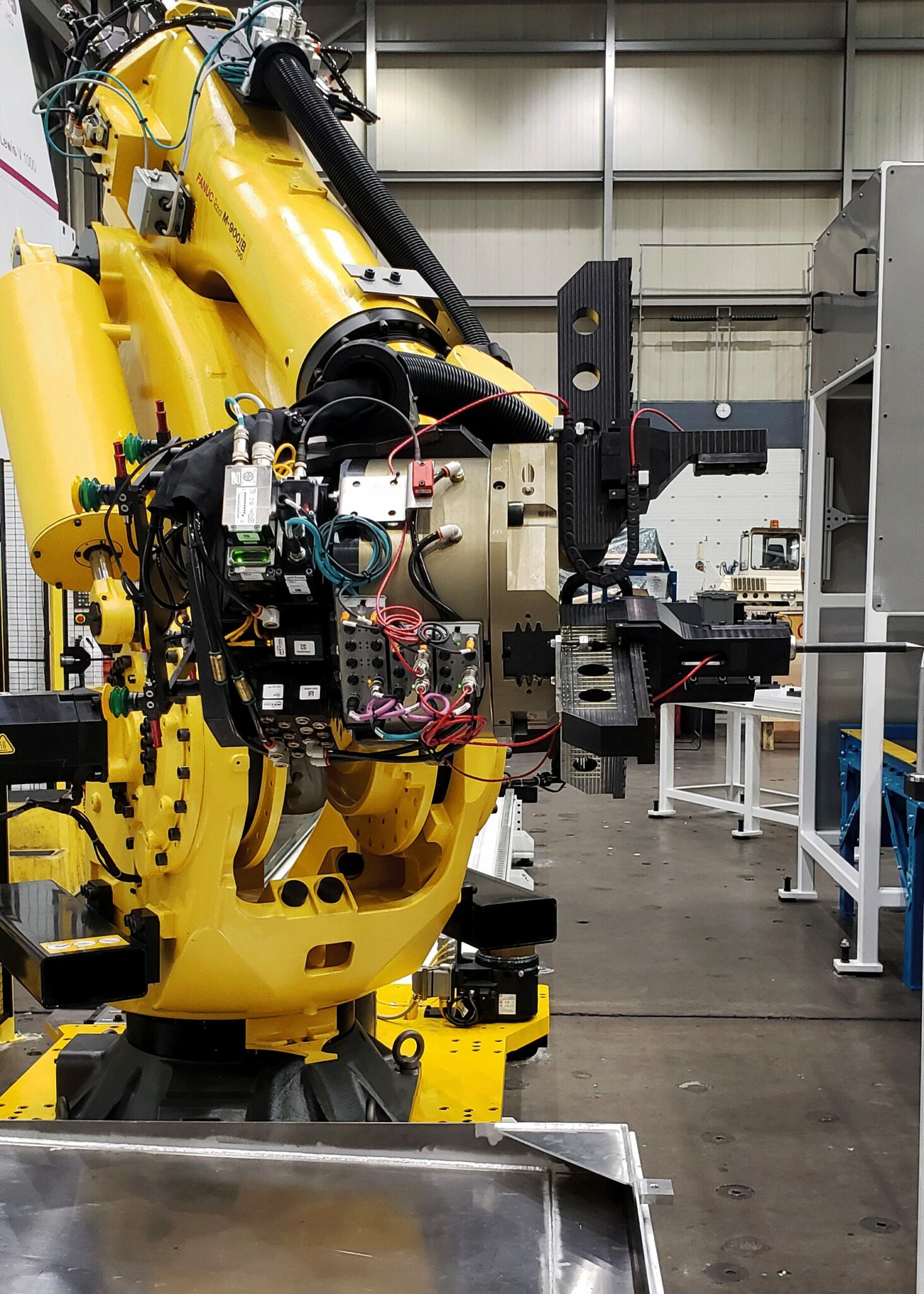
Fanuc M-900iB/700 industrial robot
The solution: Rollon RTUf
To meet this need, CNC Solutions turned to Rollon’s Steel RTUf (Robot Transfer Unit with floor mount), known for its versatility and reliability in heavy-duty applications. The RTUf is an advanced linear motion solution built to withstand demanding industrial conditions and specifically engineered to support high payloads and deliver high repeatability in positioning.
This complete robotic process automation solution features:
– High load capacity: the RTUf can handle robots of different weights and the heavy parts they manipulate, ensuring smooth, uninterrupted movement even under extreme loads.
– Precision: the RTUf maintains stability, which is critical when handling heavy parts with large industrial robots.
– Customizable configuration: the RTUf allows for extensive customization. In this project, CNC Solutions worked closely with Rollon to design a bolt pattern that suited their specific assembly needs. “We designed the robotic cell to include additional elements to be bolted to the saddle of the RTUf and then sent the CAD model directly to Rollon so they could include the extra bolt patterns needed, allowing us to attach additional elements securely,” explains Cory Roehl, Marketing and Technical Sales Engineer at CNC Solutions.
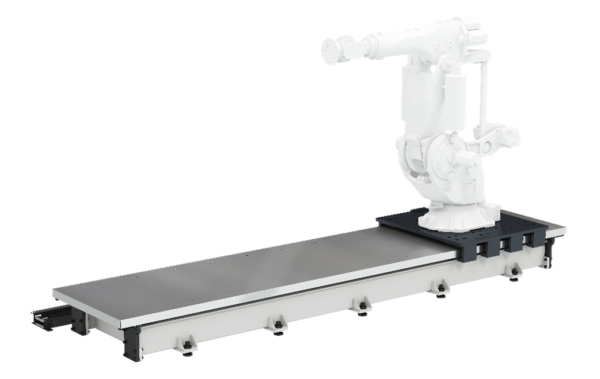
Steel RTUf

RTUf Application
The RTUf unit supplied to CNC Solutions has a stroke of 12,915 mm, is equipped with two movable saddles, and can reach a maximum speed of 3 m/s with an acceleration of 3 m/s², effectively meeting the specific requirements of the application.
Once configured, RTUf was tested on-site by CNC Solutions to ensure it met the required specifications and would function effectively in a real-world production environment. “We typically assemble and test all of our solutions to ensure everything works as expected,” says Wojtkiewicz.
The collaboration between CNC Solutions and Rollon
CNC Solutions and Rollon have a longstanding partnership based on trust and technical expertise. Their collaborative CNC automation solution development has consistently delivered exceptional results for customers across industries.
“Anytime there’s a rail involved, Rollon’s phone is going to ring,” jokes Wojtkiewicz. “We are happy in our relationship with Rollon. As an engineer, I’ve seen how their products have evolved – it’s impressive how sleek and easy to assemble they are now.”
In addition to Rollon’s products, the CNC Solutions team appreciates the efficient communication and responsive support that Rollon provides. “We need partners that are as efficient and fast as we are,” says Wojtkiewicz. “Because our work is very diverse, we rely on Rollon’s strong engineering background and adaptability to tackle each unique challenge we encounter.”
This collaborative approach enables CNC Solutions to push the boundaries of robotic automation, delivering tailored solutions that meet the stringent requirements of their customers.
Future Trends in Robotic Automation Solutions
In the future, you’ll see robotic automation solutions expanding into new territories that go beyond typical manufacturing. Companies like CNC Solutions are developing systems that combine AI vision systems with advanced linear motion technology, making it so robots can adapt to semi-structured environments.
These trends will reduce programming time while increasing flexibility, making automation accessible to businesses that have been limited by part variability or space constraints.
Conclusion
With Rollon’s RTUf, CNC Solutions successfully implemented a robust, high-capacity system for material handling in the oil and gas industry, overcoming the challenges of heavy payloads and large parts with precision and reliability. This project reflects CNC Solutions’ commitment to engineering excellence and Rollon’s capability to provide cutting-edge linear motion solutions tailored to demanding applications.
As CNC Solutions continues to expand its capabilities in robotic automation, its strong relationship with Rollon will remain a cornerstone of its success, enabling the company to address increasingly complex challenges with speed, precision, and performance.
For more information on Rollon’s linear motion solutions and to connect with Rollon application engineers in your area or region visit rollon.com.