For laypersons asked to describe an automated factory, six-axis and SCARA robots might come to mind first. But for many operations in industrial settings, automated tasks are best executed with cartesian (stacked linear) machine assemblies. That’s because linear motion systems often outperform six-axis robotics in applications involving long strokes, heavy loads, high dynamics, and tight installation spaces. In many cases, they’re also the more economical solution.
In many cases, cartesian systems outperform conventional six-axis robots and enable forms of industrial automation that would otherwise be impossible.
In fact, to underscore their overlapping suitability with six-axis robots, some industrial-component suppliers refer to stages, tables, and gantries based off linear technologies as cartesian robots — especially where these designs execute complicated multi-axis or fully automated functions.
Linear motion systems cover long distances and large workcells — serving multiple stations better than six-axis robotics.
Automated equipment based on linear assemblies outperforms robotics in applications needing to tend multiple workstations with one machine. That’s because robots are by default stationary and unable to traverse long distances. In contrast, linear axes can be designed around motor-driven rack and pinion sets for theoretically endless strokes. These linear drives nimbly move end effectors and payloads between adjacent machining stations, assembly areas, and other workcells.
Executing all these automation tasks with robotics (save for arms mounted to seventh-axis linear systems) often necessitates a whole fleet of robots that consume copious plant floorspace and incur high upfront cost.
Linear motion systems are extremely versatile, efficient, and compact with some capable of transporting payloads through several processing stations arranged in a row.
Linear motion systems excel at transporting heavy, delicate, and high-throughput loads.
Because the rotary-to-linear mechanical drives of linear actuation take so many forms, cartesian systems can be tailored to a wide array of design requirements. Case in point: Cartesian motion systems tasked with moving heavy payloads through 3D space (even over several meters and beyond) typically integrate rack and pinion drives. These drives maintain high stiffness to position heavy payloads with precision over long distances.
Read about this tire-bead production application for an example of a long-stroke heavy–payload application.
Where cartesian systems are tasked with quietly and quickly transporting many workpieces (often to support high throughput) the axes often integrate belt drives. That’s because belts are capable of highly dynamic motion — with speeds to 5 m/sec and accelerations to 50 m/sec2 for extremely short cycle times sans settling-time issues.
Finally, cartesian systems that move very delicate parts through precision processes often integrate ballscrew drives. The low-friction movement of rolling ball bearings within the ballscrew assembly make for high accuracy as well as repeatability to ±5 μm.
Cartesian systems take various forms and can concurrently run multiple tasks.
In contrast with six-axis robotics, cartesian systems allow multiple shuttles to use a given linear axis to execute tasks in tandem. Most common are machines with a horizontal Y rail (typically an overhead gantry) off which multiple vertical Z axes (and their end effectors) hang and traverse.
Where a bridge-type structure isn’t compatible with a given application, actuators can take the form of linear stages complete with reinforced frames and dual-profile linear rails (instead of single-profile variations) to function as cantilevered axes. In fact, cartesian systems can also actuate X axes off a Y axis and even multiple Y axes off a vertical Z axis.
Cartesian systems provide unmatched tandem-task capabilities.
Read about one custom linear motion design — a three-axis cartesian robot that executes machine-tending tasks on plastic injection-molding machines — by clicking here. The design was engineered for captive in-house use by an injection-molding plant operator. By integrating three different linear actuators, the operator optimized a build that’s far more compact than any standard robot having comparable motion capabilities.
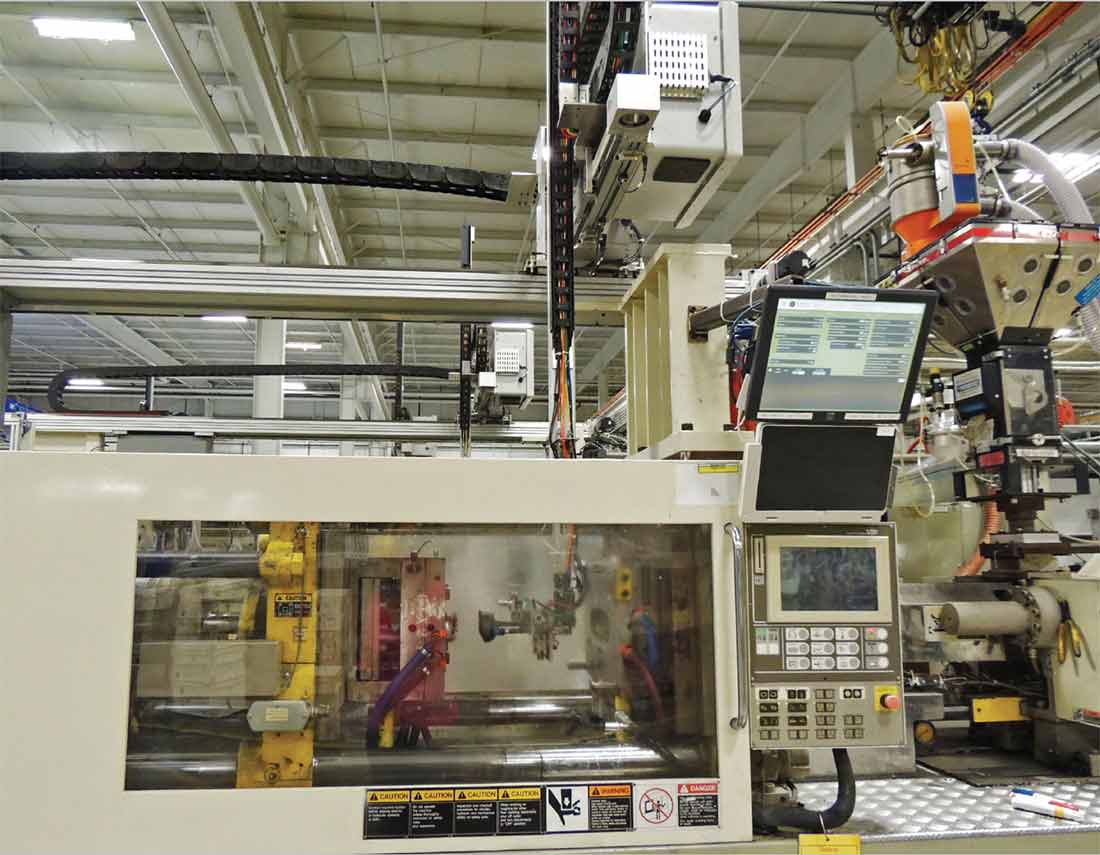
The three-DOF cartesian machine shown here employs Rollon R-SMART 160 SP6, 120 SP4, and 65 SP linear actuators for high load capacity and compactness.
Because every axis’ carriage features its own motor drive, multi-axis cartesian systems can control each either independently or via fully synchronous command routines. That’s true whether the axes are assembled in a traditional XYZ arrangement or include multiple Z axes on a gantry-type build. The latter can move loads separately or in groups (especially for pick-and-place routines) or concurrently execute completely different tasks in different areas of the production process.
Linear motion reach is more customizable than that of general-purpose robotics.
Every axis of a linear motion system can be customized by drive type (as already described) as well as length. More specifically, linear components and actuators can be specified with the exact stroke needed to satisfy the application’s reach requirements and no more. That’s useful because:
- It helps engineers trim cost by avoiding the purchase of systems (such as robotics) with reach that’s excessive for the application.
- It allows the motion solutions to fit into tight spaces within machines.
What’s more, some linear motion systems incorporate moving profile or telescopic stages and other assembly features to extend into work volumes that need to be totally cleared before the next operation cycle begins. For example, Rollon omega belt actuators often serve on Z axes to temporarily enter a workspace and tend, assemble, or otherwise service workpieces from above before retracting. Rollon’s telescopic actuators can also be used in a similar fashion when there are ceiling restrictions.
Some automated tasks are best served by linear motion systems.
Unless an application involves exceptionally exacting accuracy and throughput requirements only satisfied by a six-axis robot, design engineers should consider a cartesian-type motion design. The latter often provides unbeatable performance in automotive, packaging, machine building, logistics, and food and beverage applications involving heavy payloads, long trajectories, and confined spaces. More specifically, cartesian robots excel in uses related to:
- Parts handling.
- Workpiece transport.
- Palletizing.
In these applications, linear-system strengths include superior dynamics, reach, load capacities, and design freedom; lower upfront costs; and ease of installation and maintenance.
Case in point: Packaging tasks involving case packing and palletizing don’t typically require exceptional accuracy but they do involve heavy loads. (Check out this Rollon blog detailing specific requirements.) Any six-axis robot tasked with executing case packing and palletizing tasks would need to be enormous [costly and wasting valuable factory floor space]. In contrast, multi-axis cartesian solutions deftly transport heavy loads in such operations — even drawing whole pallets of goods upwards on vertical Z axes where needed. No directions of motion are necessarily subject to payload limitations, and the structures of a cartesian system can be built around existing production schemes.
For more information on automation that leverages the strengths of linear systems and those employing six-axis robots, visit rollon.com. Or to enter your own application’s parameters and explore the extensive capabilities of Rollon’s cartesian offerings, visit the myRollon Multi-Axis Systems configurator.