At Rollon, we offer customized, application-specific coating formulations that can be added to our linear guide rails, raceways, and precision bearing surfaces prior to shipment to provide additional insurance against corrosion and wear. Various alloying elements such as cobalt and boron are added to the nickel-base formula to achieve different properties, ranging from extreme corrosion resistance at one end of the spectrum to extreme hardness at the other.
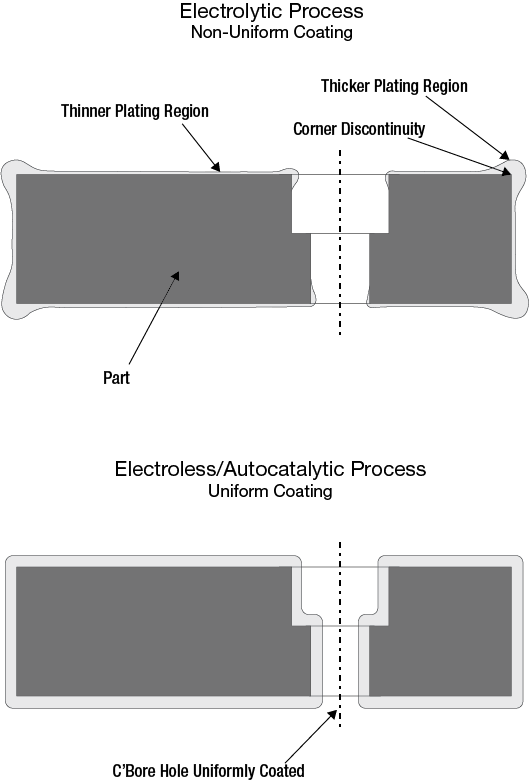
Another factor to keep in mind when considering special coatings for linear motion components is uniformity. The EN process applies nickel plating in a nearly perfect manner, achieving uniform thickness within millionths of an inch. This is not possible with electrolytic processes that tend to build up plating at the corners of surfaces, resulting in a “dog bone” effect that can be detrimental to achieving smooth, high-speed motion. Another benefit of the EN process versus electrolytic plating is the ability to coat all surfaces of the complete motion assembly—including counter-bored bolt holes that can rapidly corrode if not coated.
For your next application requiring precise motion and extreme durability, consider adding an EN coating to your bearing surfaces and linear motion components. Rollon engineers can help you select the exact EN formula to meet very specific requirements for corrosion and wear resistance. Keep in mind that nickel plating can be applied to a variety of metal surfaces, including bearing steel and aluminum, achieving 1.3 to 3´ the corrosion resistance of 440C stainless steel.