Static Load vs Dynamic Load
Data sheets and catalog pages for rolling element linear bearings or actuators provide two load capacity specifications — static load capacity and dynamic load capacity. These ratings can have a significant impact on your choice of linear bearing. It’s important to understand the differences between these two specifications so that you can properly evaluate and select an ideal bearing for your application. Note that some actuators may list a maximum force instead of a static capacity.
Understanding Static Load Capacity
Definition of Static Load Capacity
Static load capacity refers to the amount of a load the bearing can support in a given non-moving instance. This specification is typically designated as the symbol C0 and is measured in units of force, such as Newtons (N).
Importance of Static Load Capacity in Applications
The static load capacity is an important factor to consider when evaluating whether a system can withstand shock loads, repeated loading and unloading, and emergency stop conditions. If a bearing is subjected to a load that exceeds its static load capacity, the raceways may develop brinelling, resulting in noisy operation and premature failure. It is therefore crucial to choose a bearing with a static load capacity that is appropriate for your application’s needs.
How Static Load Capacity Was Defined
Historical Definition of Static Load Capacity
For many years, the basic static load capacity in a rolling element bearing was defined as the amount of load that would result in a permanent deformation of the rolling element equal to 0.0001 times its diameter.
Updated Standard
However, the standard has been updated to specify a load amount that can cause 480,000 pounds per square inch (psi) [3,310 megapascals (Mpa)] of Hertzian contact stress in the raceway. Regardless of how it is defined, be sure to check your static capacity safety factor using the following formula and guidelines:
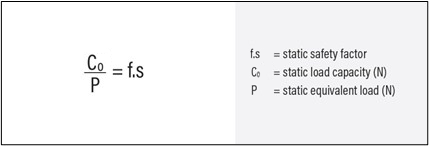
- Under normal load and operating conditions: f.s = 1-2
- Under impact load or vibration operating conditions: f.s = 2-3
- For best dynamic performance and service life, aim for a f.s >5.
Understanding Dynamic Load Capacity
Definition of Dynamic Load vs Static Load
Dynamic load capacity is not a stand-alone load rating, but rather a parameter used in an equation to calculate the theoretical service life of a bearing system. It is typically defined as C and specified in force units of N. At Rollon, our dynamic load capacity corresponds to a nominal service life of 100 kilometers of linear travel in accordance with DIN ISO 14728-1 in the United States and Europe. In some regions, the nominal service life is based on 50 kilometers.
Comparing Static and Dynamic Load Values
When comparing static and dynamic load values, consider the lowest value of the two as a starting point when assessing the bearing’s ability to carry the expected load. When specifying a bearing, it’s important to already know the weight of your static load and possibly your lifetime requirement, too. This information, along with the dynamic load rating, will help determine the lifetime capacity of the linear bearing system.
In most situations, multiple forces will act on your bearing. For example, if you anticipate a load that is 50 percent of the static load and also expect to see twisting, moment or other types of load, the lifetime calculation equation will incorporate these values as part of a single effective equivalent load value — P.eq, or just P.
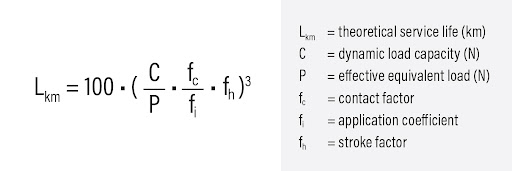
Use the Dynamic Load Rating To Calculate the Service Life
Rollon Linear Line and Service Life Formula
Rollon’s Linear Line of guides features a broad selection of product families like our Compact Rail, Compact Rail Plus with a double row of ball bearings, and Mono Rail profiled rail with recirculating ball bearings. When calculating the service life of our Linear Line, we use the following formula:
Expert Support for Accurate Calculations
We recommend talking to our experts to ensure accurate calculations. Our team will gather the relevant details about your application and ask the necessary questions to determine the appropriate service life calculation for your bearing. We will consider variables such as multiple bearings, environmental factors, and stroke distance, which can affect service life..
Factors Impacting Bearing Service Life
Environmental and Operational Considerations
Load factors are determined by taking into account all the loads that the linear bearing is expected to encounter in its application. When calculating service life, it’s essential to consider additional variables that can impact the bearing’s lifetime, such as the use of multiple bearings, environmental factors such as dirt or vibrations, and the stroke distance.
Shorter strokes may not allow the slider’s internal components to completely recirculate. This can prevent the reapplication of the lubricant on the bearing surfaces and therefore increase the likelihood of excessive friction and premature failure.
Rail Protection Options
For applications in corrosive environments, consider Rollon’s range of rail protection options before calculating service life. Our catalogs include look-up charts that enable you to factor in these variables when making your calculations. Moreover, if you expect your bearings to operate in a corrosive environment, consider Rollon’s many rail protection options before calculating service life
Gain Clarity to Select the Most Reliable Bearing
While static load capacity is a fundamental factor when sizing, buying and specifying any linear bearing, a proper understanding of dynamic load capacity is critical to ensuring it will perform reliably over its lifetime without incurring rail damage or failure.
At Rollon, we offer a wide range of quality bearings that can meet your linear motion requirements. Our engineering team can review your application details and help perform the dynamic load calculations so you can choose an ideal bearing that performs reliably over your target service life.
For more information about Rollon’s Linear Rails, visit our product pages.